〈 笔者 : 杉田直彦 〉
Naohiko Sugita:东京大学 大学院工学系研究科 教授
截至2024年,制造行业在追求传统的高精度和高效率的同时,还面临供应链问题、劳动力短缺,以及SDGs目标中的脱碳等新挑战。例如,制造业劳动力的减少日益严重,具备技能的人才获取与培养变得愈发困难,导致制造现场对省人化和自动化的需求日益迫切。此外,高效应对多品种小批量生产、确保高精度产品的稳定生产、提升成本及交期竞争力,以及缺乏具体落实脱碳的技术等诸多问题交织在一起,使得寻找解决方案变得极为困难。在大型企业中,已引入的自动化设备未能得到充分利用,而中小企业则对自动化的导入仍持观望态度。
在这样的背景下,未来的制造业需要明确区分由人来执行的作业与可进行省人化、自动化的作业,并将两者融合。此外,行业应从单纯追求机床的单体性能,转向工厂整体的优化,乃至进一步发展至涵盖数字化服务的便利性提升。本文将在此背景下,重点介绍各大机床制造商将在日本国际机床展(JIMTOF 2024)上展示的相关技术。
自动化解决方案
Okuma提供多种自动化解决方案。“Green-SmartMachine”作为支持自动化的智能机床,实现了无需依赖人工操作和技能,即可自主稳定维持高精度,同时兼顾高生产率与脱碳、省能。此外,机器人加工单元可灵活应对多品种小批量生产,且机床操作员可轻松上手。此外,公司还提供提升单位面积生产效率的紧凑型自动化方案、自动化过程中不可或缺的切屑处理性能优化方案,以及助力高精度加工自动化的质量管理解决方案。
1.Green-Smart Machine
在自动化环境下,由于作业人员通常不在现场,因此机床的可靠性和精度稳定性至关重要。Green-SmartMachine 采用智能化技术“Thermo-Friendly Concept”,使机床能够自主稳定地维持高精度。此外,借助“ECOsuite plus”节能技术,机床可根据自身精度状态判断冷却需求,在保持高精度的同时,实现冷却装置的空闲停机(Idle Stop)。这一技术可在不中断生产的情况下,自动维持高精度并节能,无需人工介入或特定技能支持。
2.移动式协作机器人加工单元(图 1)
移动式协作机器人OMR系列最多可注册10台加工机和30种工件,可根据生产量的变化快速自动化所需机床与工件。此外,该机器人无需示教或编程,即使不具备专业知识和技能的操作人员也能轻松使用。机器人配备的视觉传感器可自动补偿机器人与加工机之间的相对位置变化,因此重新安装后无需重新示教。新工件的注册仅需输入参数,显著缩短了自动化启动时间,并减轻了作业人员的负担。已注册的加工机和工件的自动化设定时间约为4分钟。此外,即使因车削中心(车床)与加工中心(MC)切换导致工件形状发生变化,调整存储架上的夹具板仅需1分钟。因此,该系统能够根据日常变化灵活迅速地实现加工机的自动化,适用于小批量自动化、夜间自动化以及人与自动化系统共存的多品种生产环境。
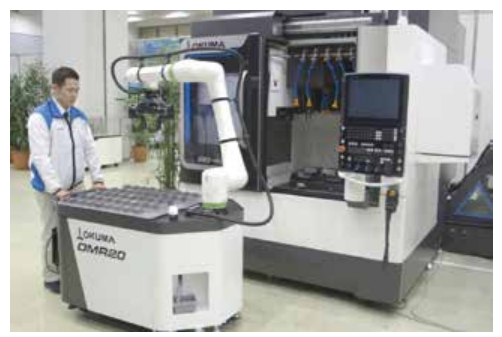
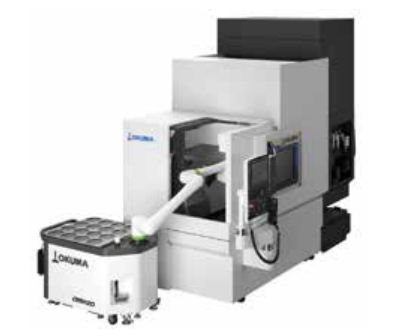
3.切屑处理性能优化的自动化系统
稳定的自动化生产需要高效的切屑处理。加工室内的切屑堆积可能导致工件装夹不良或移动盖板损坏等问题,即使引入自动化系统,也可能需要人工干预、暂停生产并清理机内切屑。为了解决这一问题,公司开发了一款具备高效切屑处理性能的小型卧式加工中心(MC),其结构可迅速回收切屑并将其排出机外。此外,该系统可根据用户的生产方式,与装载机、机器人以及AWC(AutoWorkpiece Changer)自动工件更换装置等配合使用,在确保作业空间的同时,构建最优且紧凑的自动化系统(图2)。
数字化轮廓磨床
轮廓磨床(如图3所示)是一种通过在机上投影工件和砂轮,并使砂轮沿垂直方向运动来加工模具零件或刀具等工件的机床。其底座部分采用高精度、高刚性的结构。借助高精度投影仪,在测量工件与图纸的偏差的同时进行加工,从而实现高精度加工。然而,在传统的模拟轮廓磨床中,由于测量依赖于作业人员的目视观察,不同操作者的熟练度差异会导致加工精度的波动。近年来,随着工业相机可搭载高像素CMOS相机,即使是非熟练操作人员也能实现高精度加工,因此轮廓磨床逐步实现数字化。数字化使得多种新功能得以应用,其中之一便是和井田制作所(Waida MFG)的AR 砂轮显示功能。如图4所示,该功能可将砂轮测量所得的轮廓形状叠加显示在实际图像上,即使砂轮因阴影遮挡而无法直接观察,也能通过 AR 砂轮显示功能清晰可见。此外,由于加工过程中砂轮会沿垂直方向移动,可能会偏离焦点,但借助AR 砂轮显示功能,即使在加工中也能随时确认砂轮的位置。
此外,该公司开发的高亮显示功能针对投影仪在工件轮廓与基准线对齐时存在的难题,将CAD图线条的对准情况以颜色变化的方式呈现,从而消除了因目视对准带来的误差。当工件的边缘进入CAD图设定的检测区域时,颜色会发生变化,以便操作者判断是否对齐,因此即使是非熟练人员也能轻松操作。
在投影仪测量时,由于砂轮无法清晰呈现,因此在创建示教程序时难以准确绘制加工轨迹。传统方式通常是先在大致位置对准砂轮,进行试切后再观察工件加工情况并调整轨迹。为了解决这一问题,结合AR砂轮显示功能和高亮显示功能,开发出了能够简化示教程序创建的数字示教功能。此外,还开发了可实时对比CAD图与工件边缘,并以放大方式呈现偏差的实时间隙显示功能。
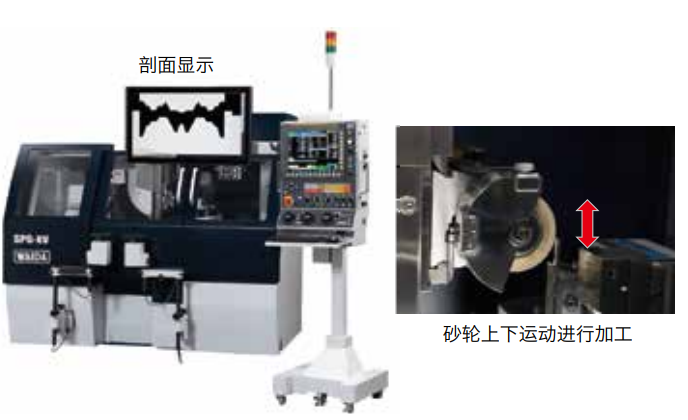
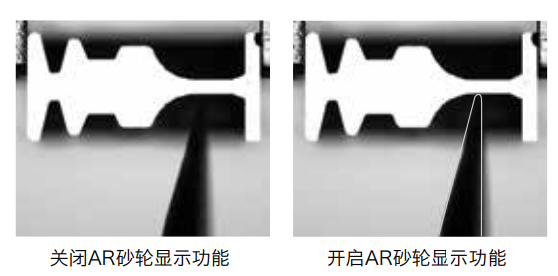
磨削加工的复合化
随着对将专用机功能集成至复合加工机、进一步强化工序整合的需求不断增加,山崎马扎克(YamazakiMazak)已在其复合加工机「INTEGREX」中引入了金属增材制造(AM)、搅拌摩擦焊接(FSW)以及齿轮加工功能。本次更进一步,将磨削加工功能集成其中。为了在复合加工机上实现磨削加工,首先需要保护机床免受磨削过程中产生的碎屑影响。磨粒脱落后形成的硬质细小切屑尺寸通常小于10μm,比切削加工所产生的切屑更微小。此外,磨粒及被加工材料的硬度通常较高。为防止这些高硬度微小切屑及磨粒对机床造成损害,该设备强化了机内的防尘性能,并采用了数微米级的过滤系统(图5)。此外,机床内部的冷却液箱配备了搅拌装置,可防止磨粒和切屑凝结成泥状沉积物(污泥)。
除了防尘和切屑处理功能,该设备还配备了专门用于磨削加工的功能,包括机内修整循环和砂轮与工件的接触检测功能。机内安装了单点金刚石修整器,并开发了专门的编程辅助软件,以简化修整轨迹的编程。操作者只需按照图形化引导界面输入砂轮尺寸等关键参数,即可完成编程。
如图 6所示,该复合加工机实现的磨削表面粗糙度约为Ra 0.2,并且在某些情况下甚至可获得更高光洁度的镜面效果。加工尺寸的波动控制在数微米范围内。具备这些性能与功能的复合加工机,有望实现对更多零部件的加工工序一体化。未来,集成磨削功能的复合加工机预计将在进一步自动化的方向上持续发展。
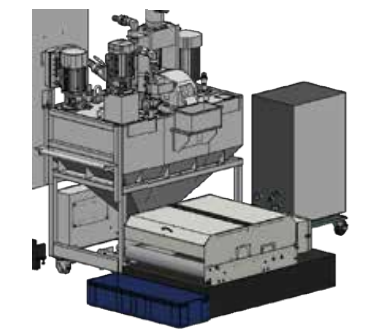
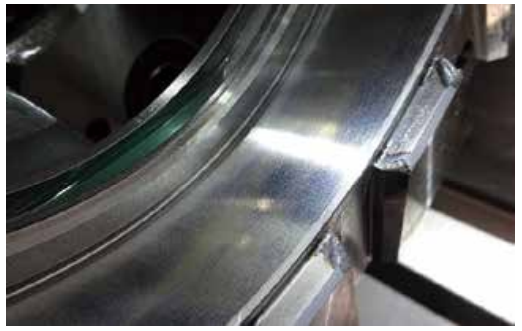
缩短加工时间的复合加工机
制造现场面临的最大课题是“交期与成本”。近年来,受工作方式改革和新老交替带来的劳动力短缺影响,企业必须在较少人手的情况下创造利润。为解决这一问题,中村留精密工业将在JIMTOF2024展会上推出专注于高速加工的新产品,以及可解决切屑问题的软件等解决方案。
1. 复合精密CNC车床「V系列」
具备全新概念的复合精密CNC车床(图7)搭载了自主研发的软件「Chronocut」。该软件通过优化主轴同步、刀塔旋转、原点复归、C轴定位与制动等非切削时间(Idle Time),实现高速化。由于不改变加工条件,因此不会影响加工精度。此外,进给轴的加减速性能得到提升,使其更快达到最高速度,从而加快启动与停止的动 作。此 外,铣 削主轴的最 高转 速 提升至10,000rpm,从而缩短加工时间。
结合Chronocut的高速化效果,与传统设备相比,面取加工(铣削:6,000rpm)所需时间由45.6秒缩短至18.6秒(10,000 rpm)。铣削主轴的扭矩也提升至24.0 Nm,而R侧主轴则提升至18.5 Nm。除了转速提高,扭矩的增强使加工条件更加优化。
2. 切屑分断功能「Triangle Cut(三角切削)」
由于切屑缠绕导致的加工缺陷是制造现场的重要课题。金属切削过程中产生的切屑可能缠绕在刀具或工件上,从而导致产品表面受损,或阻碍冷却液到达加工点,影响加工稳定性。为解决切屑缠绕问题,此前曾提出高压冷却液或摆动切削等切屑分断方法。每种方法均有其优缺点,因此用户需根据所使用的机床和加工条件选择最合适的方案。
新开发的切屑分断功能「Triangle Cut(三角切削)」(图8)通过让车削加工路径呈三角形运动,在加工过程中主动分断切屑。刀具在三角形轨迹运行时会周期性地离开工件表面,形成空切(Air Cut),确保切屑被有效分断。由于Triangle Cut的低频运动特性,它也适用于滑动导轨机床。此外,该功能能够在不显著降低表面粗糙度的情况下进行切屑分断,从而获得接近普通车削的表面质量。另一方面,由于加工路径延长,Triangle Cut可能会使加工时间增加至原来的2.7~3倍,这一点是其主要缺点。
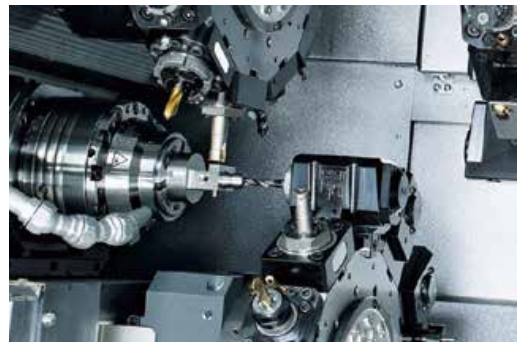
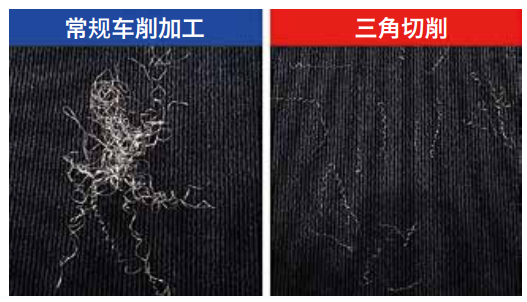
新型CNC系统的提案
FANUC 结合 IoT、AI、数字技术及机器人技术,提出了一种全新的 CNC 系统¹)。CNC 和伺服系统的设计从零开始进行重新审视,使工作机械在设计阶段即可实现优化,从而进一步提升加工性能和操作便利性。此外,伺服电机、主轴电机及其驱动放大器在能效方面取得了显著提升,以应对环境负荷问题。
1.最新 CNC「FS 500i-A」
FANUC 结合 IoT、AI、数字技术及机器人技术,提出了一种全新的 CNC 系统¹)。CNC 和伺服系统的设计从零开始进行重新审视,使工作机械在设计阶段即可实现优化,从而进一步提升加工性能和操作便利性。此外,伺服电机、主轴电机及其驱动放大器在能效方面取得了显著提升,以应对环境负荷问题。
该最新 CNC 设备相比上一代高端机型 30i-B Plus,CPU 处理性能提升至 2.7 倍,图形处理能力也得到增强(图 9)。此外,接口方面亦进行了升级,标配 3 个千兆以太网端口,同时提升了 FSSB(FANUC Serial ServoBus)的通信性能与可靠性。该设备还实现了无电池化设计,提升了维护便利性,并且通过单元的标准化设计,使组件拆卸更加简单。
CNC 与伺服系统的组合至关重要,搭配全新的 αi-D系列伺服系统后,可最大化提高伺服系统的高速性、精度及能源效率。该伺服系统可在较低电流下实现相同的扭矩输出,并根据运行条件进行最优电流控制。此外,采用最新的低损耗功率半导体和新型低损耗 AC 电抗器,使机床的节能性能进一步提高。
2.新型 CNC 与多轴控制机床
FANUC Series 500i-A 采用了全新的软件架构,可自由控制 5 轴、6 轴及以上的轴配置。在 CNC 运行过程中,系统根据程序指令执行运动学变换,以生成机床各轴的具体运动轨迹。在最新的 CNC 系统中,如图10所示,机床的轴配置被识别为 “机床结构树”,并基于该结构树进行运动学变换。因此,只需设置机床结构树,即可适应各种机床配置,实现高效控制。多轴机床的应用将有助于缩短加工时间,同时提升复杂形状零件的加工能力。
3.机器人加工
另一个值得关注的领域是机器人加工。目前,机器人加工的研究主要集中在欧美的科研机构,但尚未实现广泛的实际应用。其主要障碍在于机器人本体的刚性和精度较低,难以克服这一限制。然而,FANUC 擅长开发高精度、高刚性的机器人,即使在外力作用下仍能保持极高的轨迹精度,使其能够用于承受较大反作用力的加工场景。
如图 11所示,依托高刚性、高精度的机器人,以往难以实现的切削加工如今成为可能。此外,多关节机器人凭借其广阔的运动范围和高自由度,即使在有限的空间内,也能从多个方向加工大型零件。未来,有望进一步拓展至由多个自主分布式机器人协同进行大型零件切削加工等应用场景。FANUC 的机器人加工技术仍在不断发展,值得持续关注。
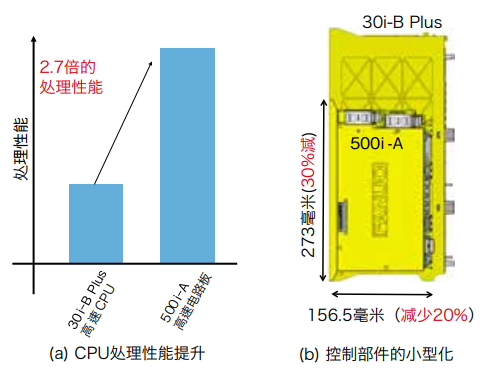
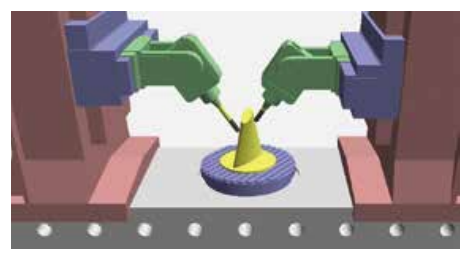
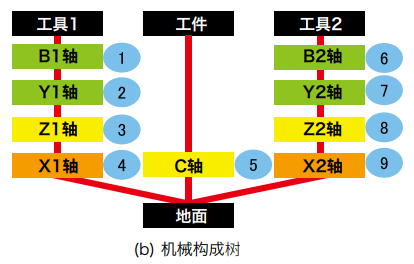
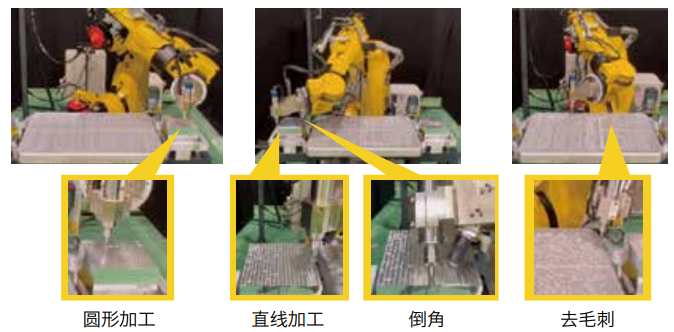
滑动导轨的机械花纹加工
工作机床的导轨需要具备足够的刚性,以承受加工力和惯性力,同时还需在保持几何精度的前提下,实现平稳的移动。滑动导轨是最早被采用的导轨方式,但近年来由于生产效率较低,使用量有所减少。然而,滑动导轨依然具备其他导轨方式所不具备的优异特性,因此仍被广泛应用于众多机床设备中。
高精度平面的刮研工艺是制造滑动导轨的核心技术,但由于该工艺耗时长,生产效率难以提升,同时作业者之间的质量差异也成为一大问题。此外,传统手工刮研所形成的凹槽较浅且不均匀,随着磨损的增加,接触区域容易发生变化,导致润滑油积聚,无法顺畅流动,从而引发运动部件的浮动及润滑不良等问题。针对这一情况,牧野铣床制作所通过将刮研工艺由手工作业转变为机械加工,以提升生产效率。
为了减少摩擦阻力,移动部件的滑动面上粘贴了树脂材料(如氟树脂、酚醛树脂),并对其进行机械加工(称为 “机械花纹加工”),如图12(a)所示。机械花纹加工可实现更深且均匀的凹槽,利用这一优势,设计了便于润滑油流动的花纹结构。通过适当控制润滑油的流动,不仅能抑制浮动现象,还能排出磨损粉末等杂质,从而实现良好的润滑状态。
在花纹设计过程中,对与轨道面接触的“接触点”数量及其面积大小进行了研究。对于英寸平方单位的接触点数量,理想范围为 20~30 个。此外,接触点的面积占比(称为“百分比接触”)以 20% 左右为最佳。
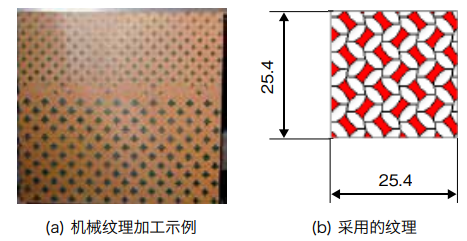
图12(b)展示了实际采用的机械花纹示例,其中英寸平方单 位的接触点数量为 28 个,百分比接触为20%。由于百分比接触会随切削深度变化,因此通过切削深度作为参数来控制花纹形态。目前,该技术已应用于该公司立式加工中心「V33i」等配备滑动导轨的机型。从开始实施至今已超过 20 年,该技术在提高滑动导轨机型的生产效率及稳定产品质量方面发挥了重要作用。
2024 年是 JIMTOF 举办之年,各家公司将展示何种机床设备备受关注。因此,本文概述了各工作机床制造商的相关举措。尽管自动化与环保对策将成为核心议题,但从下游产业的角度来看,仍需明确工作机床在汽车、工程机械、航空航天、半导体及医疗设备等行业中的定位。然而,当前形势较为复杂,仍有许多研究空间。希望日本能够进一步完善相关机制,持续保持在工作机床领域的主导地位。
参考文献
1)羽田浩二、宫崎义人、佐古田恭庸、细川匡彦、小泉彰、黑岩大:《FANUC Technical Review》,Vol.31,No.1(2023),pp.1-11